Abstract
In today’s competitive landscape, Quality Management Systems (QMS) play a pivotal role in driving operational excellence and ensuring long-term success across industries. “The Blueprint for Success: A Comprehensive Synopsis of Quality Management Systems (QMS)” delves into the fundamental concepts, methodologies, and best practices that organizations can implement to establish robust QMS frameworks. This article offers a detailed exploration of key QMS components, including process control, continuous improvement, and compliance with international standards like ISO 9001. It outlines the critical benefits of QMS, such as enhanced product quality, increased customer satisfaction, reduced operational risks, and improved efficiency.
By breaking down the principles of QMS and highlighting their role in sustaining excellence, this comprehensive guide empowers businesses to fine-tune their processes and foster a culture of improvement. Whether you’re looking to improve compliance, reduce defects, or streamline operations, this article provides actionable insights and strategies that can be applied to any organization aiming for superior quality outcomes and sustained success.
In this blog post, we will dive deep into the intricacies of QMS, its role in manufacturing, and how it can transform your operations. Whether you’re a small business looking to improve quality or a large enterprise aiming for greater efficiency, this guide will provide valuable insights into the world of QMS.
Keywords: Quality Management Systems (QMS), QMS framework, QMS best practices, process control in QMS, continuous improvement in QMS, ISO 9001 standards, QMS compliance, operational excellence through QMS, product quality improvement, customer satisfaction in QMS, risk reduction in QMS, QMS implementation, efficiency in QMS, QMS strategies, business success with QMS, quality assurance in QMS, improving quality systems, quality control methods, QMS benefits, robust QMS solutions.
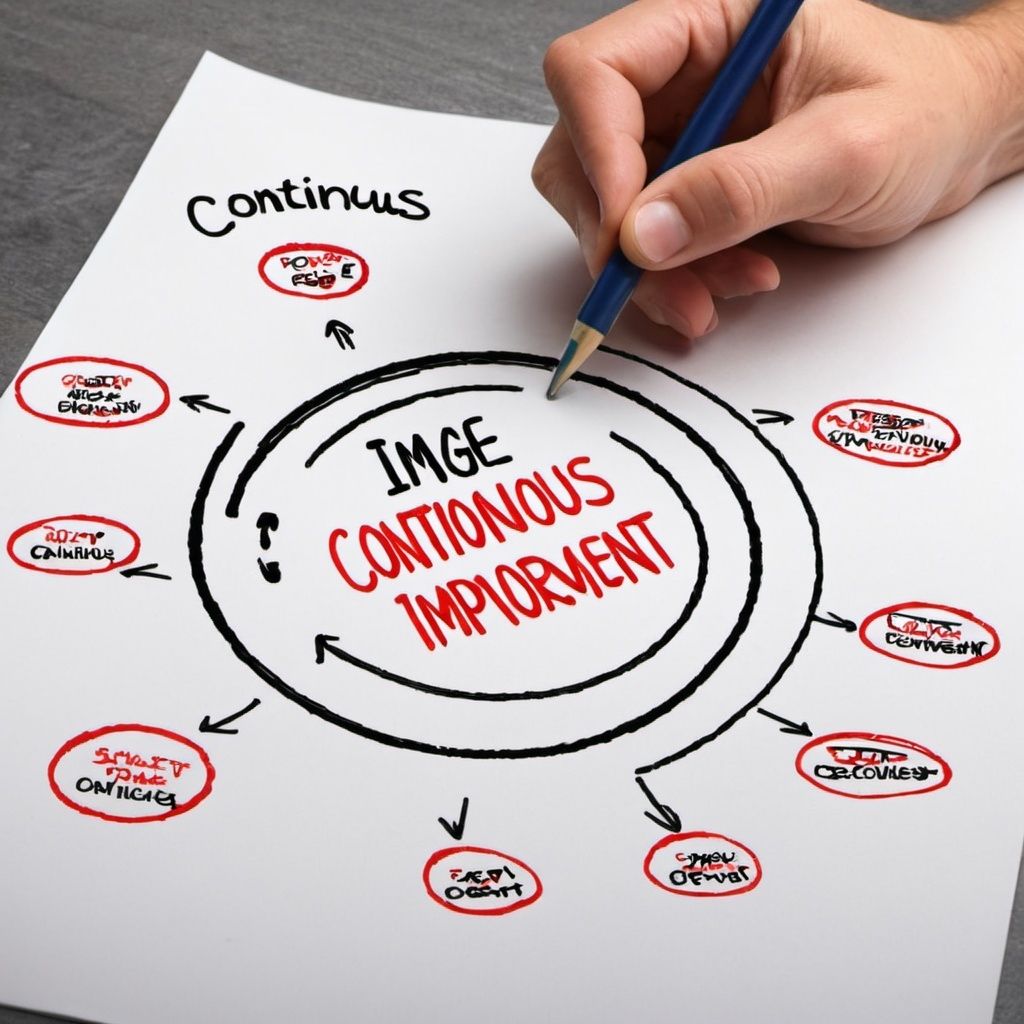
What is a Quality Management System (QMS)?
A Quality Management System (QMS) is a formalized system that documents the processes, procedures, and responsibilities required to achieve quality objectives and meet customer expectations. At its core, a QMS provides a structured approach to managing quality throughout an organization’s operations. In manufacturing, this means that every step in the production process—from raw material procurement to final product delivery—is carefully controlled and monitored to ensure it meets predefined quality standards.
Implementing a QMS in a manufacturing environment isn’t just about improving product quality; it’s about creating a culture of continuous improvement. This system allows manufacturers to minimize errors, reduce waste, and improve the efficiency of their operations. More importantly, it helps organizations meet the demands of increasingly stringent customer and regulatory requirements.
By adhering to international standards such as ISO 9001, manufacturers can not only improve their internal processes but also gain a competitive edge in the global marketplace. ISO 9001, one of the most widely recognized QMS standards, provides a comprehensive framework for organizations to manage quality systematically.
Core Principles of Quality Management Systems
The success of a QMS hinges on several foundational principles. These guiding principles form the backbone of any effective quality management system, ensuring that quality improvement is not a one-off initiative but an ongoing, integrated part of daily operations.
1. Customer Focus
A customer-centric approach is at the heart of every successful QMS. Every decision made, every process implemented, and every product produced should aim to satisfy customer needs and expectations. Customers today are more demanding than ever, expecting high-quality products delivered quickly and efficiently. A QMS ensures that these expectations are met consistently, and even exceeded, by aligning the organization’s objectives with the needs of its customers.
2. Leadership and Employee Involvement
Effective leadership is crucial for the success of a QMS. Leaders must not only set the vision for quality management but also inspire and empower their employees to take ownership of the quality process. Employee involvement is critical; when workers are engaged and feel responsible for the quality of their work, they are more likely to contribute to continuous improvement efforts. Involving employees in the decision-making process can lead to valuable insights and innovative solutions that might otherwise be overlooked.
3. Process Approach
A QMS emphasizes a process-oriented approach to quality management. This means that organizations must view their operations as interconnected processes rather than isolated tasks. Each process, whether it’s production, procurement, or delivery, must work seamlessly with the others to achieve the desired outcome. By focusing on process optimization, manufacturers can reduce variability, eliminate bottlenecks, and ensure that resources are used efficiently.
4. Continuous Improvement
Continuous improvement is one of the most critical principles of a QMS. It encourages organizations to constantly evaluate their processes and find ways to improve them. In a rapidly changing market, manufacturers must remain agile and adaptive to stay ahead of the competition. Continuous improvement ensures that organizations are always looking for ways to enhance their product quality, reduce waste, and improve customer satisfaction.
5. Data-Driven Decision Making
In today’s data-rich environment, making decisions based on intuition alone is no longer sufficient. A QMS relies heavily on data-driven decision-making. This means that decisions should be based on accurate and timely data that provide insights into key performance metrics such as defect rates, cycle times, and customer feedback. Data-driven decision-making reduces the risk of errors and ensures that resources are allocated where they will have the most significant impact.
6. Supplier Relationship Management
The quality of raw materials and components used in manufacturing has a direct impact on the final product’s quality. A QMS emphasizes the importance of building strong relationships with suppliers to ensure they provide high-quality materials consistently. This involves setting clear quality expectations, conducting regular supplier audits, and fostering open communication to resolve any issues quickly.
The Role of QMS in Manufacturing Organizations
The role of a Quality Management System in manufacturing is multifaceted. It’s not just about ensuring that products meet specific quality standards—it’s about creating a system that enhances overall efficiency, reduces waste, and drives customer satisfaction. A well-implemented QMS provides the tools and processes necessary for manufacturers to monitor, control, and improve their production activities.
1. Ensuring Consistent Product Quality
One of the primary roles of a QMS is to ensure consistent product quality. In a competitive market, consistency is key. Customers expect the same level of quality in every product they purchase. A QMS helps manufacturers achieve this by standardizing processes and establishing clear quality benchmarks. With a QMS in place, defects and variations in product quality can be identified and addressed early in the production process, preventing costly rework or product recalls.
2. Enhancing Operational Efficiency
A QMS also plays a critical role in improving operational efficiency. By identifying inefficiencies and areas of waste, manufacturers can streamline their operations, reduce lead times, and lower production costs. This is particularly important in industries where margins are tight, and even small improvements in efficiency can have a significant impact on profitability. A QMS promotes a culture of continuous improvement, ensuring that processes are regularly evaluated and optimized for maximum efficiency.
3. Driving Customer Satisfaction
Customer satisfaction is at the core of any successful manufacturing business. A QMS ensures that products meet or exceed customer expectations, leading to higher levels of customer satisfaction and loyalty. Satisfied customers are more likely to become repeat buyers and recommend the company to others, helping to drive growth and profitability. By focusing on quality at every stage of the production process, manufacturers can build a reputation for reliability and excellence.
4. Ensuring Compliance with Regulatory Standards
Manufacturers are subject to a wide range of regulatory requirements, depending on the industry they operate in. A QMS helps organizations ensure compliance with these regulations by providing a structured approach to managing quality and documenting processes. This not only reduces the risk of non-compliance but also makes it easier for manufacturers to pass audits and maintain certifications, such as ISO 9001, which are often required by customers and regulatory bodies.
Key Components of an Effective QMS
An effective Quality Management System comprises several key components that work together to create a seamless framework for managing quality.
1. Documentation and SOPs
Clear and concise documentation is essential for the success of any QMS. This includes standard operating procedures (SOPs), work instructions, and quality manuals that define how processes should be carried out. Proper documentation ensures that all employees understand their roles and responsibilities and that processes are followed consistently.
2. Quality Control and Quality Assurance
While quality control (QC) focuses on identifying defects and ensuring that products meet quality standards, quality assurance (QA) is about preventing defects from occurring in the first place. Both QC and QA are essential components of a QMS, working together to ensure that products are manufactured to the highest standards of quality.
3. Continuous Monitoring and Auditing
A robust QMS includes mechanisms for continuously monitoring and auditing processes. Regular audits help identify areas for improvement and ensure that the QMS is being followed as intended. Monitoring key performance indicators (KPIs) such as defect rates, production cycle times, and customer complaints provides valuable insights into the effectiveness of the QMS and where adjustments may be needed.
4. Corrective and Preventive Actions (CAPA)
The CAPA process is an essential part of a QMS. It involves identifying the root cause of any issues, implementing corrective actions to resolve the problem, and taking preventive measures to ensure the issue doesn’t occur again. By addressing problems proactively, manufacturers can improve the overall effectiveness of their QMS and prevent recurring issues.
Popular QMS Standards in Manufacturing
There are several widely recognized standards that manufacturing organizations can adopt to implement an effective QMS.
1. ISO 9001
ISO 9001 is the most popular and widely recognized QMS standard globally. It provides a framework for organizations to ensure that their products and services consistently meet customer and regulatory requirements. By adopting ISO 9001, manufacturers can improve their internal processes, enhance customer satisfaction, and gain a competitive edge in the marketplace.
2. Six Sigma and Lean Manufacturing
Six Sigma and Lean Manufacturing are methodologies that complement ISO 9001 by focusing on reducing variation (Six Sigma) and eliminating waste (Lean Manufacturing) in processes. These approaches help manufacturers improve quality while reducing costs, making them valuable additions to any QMS.
3. Industry-Specific Standards
In addition to ISO 9001, specific industries have their own QMS standards. For example, the IATF 16949 standard is used in the automotive industry, while the **AS9100
FAQs about Quality Management System (QMS)
The main purpose of a Quality Management System (QMS) is to ensure that an organization consistently produces products or services that meet or exceed customer expectations. It provides a structured framework for managing and improving the quality of processes and products, ensuring compliance with industry standards and regulatory requirements. By implementing a QMS, organizations can enhance operational efficiency, reduce errors, and drive continuous improvement.
A QMS benefits manufacturing organizations in several ways:
- Consistency: It ensures that products are produced to the same quality standards, reducing defects and variations.
- Efficiency: By streamlining processes and eliminating waste, a QMS improves overall operational efficiency.
- Compliance: A QMS helps organizations meet regulatory and industry-specific standards, such as ISO 9001, which is crucial for staying competitive.
- Customer Satisfaction: Consistent quality leads to higher levels of customer satisfaction, which can drive repeat business and brand loyalty.
- Cost Reduction: Reducing rework, waste, and inefficiencies lowers production costs and improves profitability.
The key elements of a QMS include:
- Documentation and Standard Operating Procedures (SOPs): Clear, well-documented processes to ensure consistency.
- Quality Control (QC) and Quality Assurance (QA): QC focuses on identifying defects, while QA works to prevent defects from occurring.
- Continuous Monitoring and Auditing: Regular monitoring and audits ensure that the QMS is effective and highlight areas for improvement.
- Corrective and Preventive Actions (CAPA): CAPA addresses any issues in the process and implements measures to prevent their recurrence.
- Leadership and Employee Involvement: Active engagement from leadership and employees is crucial for the success of a QMS.
ISO 9001 is an international standard for Quality Management Systems (QMS). It provides a comprehensive framework for organizations to ensure that their products and services consistently meet customer and regulatory requirements. For manufacturers, ISO 9001 is crucial because it helps build trust with customers, ensures compliance with legal requirements, and enhances operational efficiency. Certification to ISO 9001 demonstrates a commitment to quality and continuous improvement, which can provide a significant competitive advantage.
Quality Assurance (QA) and Quality Control (QC) are both essential components of a QMS, but they serve different purposes:
- QA is a proactive process that focuses on designing and improving processes to prevent defects before they occur. It ensures that the manufacturing process is capable of consistently producing high-quality products.
- QC, on the other hand, is a reactive process that involves inspecting and testing products after they are produced to identify any defects or deviations from quality standards. QC ensures that only products that meet the required specifications are delivered to customers.
A QMS helps organizations meet regulatory requirements by providing a structured approach to managing quality, documenting processes, and ensuring that operations align with applicable standards. In many industries, compliance with standards such as ISO 9001, IATF 16949 (automotive), or AS9100 (aerospace) is essential to operate legally and maintain customer trust. Regular audits, both internal and external, ensure that the organization adheres to these standards and continuously improves its processes to meet regulatory demands.
A QMS is beneficial for almost all industries, particularly in manufacturing sectors. Industries such as automotive, aerospace, pharmaceuticals, electronics, food and beverage, and medical devices require strict adherence to quality standards due to regulatory requirements and the need for high-quality, reliable products. However, even industries outside manufacturing—like healthcare, education, and service-based businesses—can implement a QMS to improve efficiency, reduce errors, and enhance customer satisfaction.
Implementing a QMS doesn’t have to be overwhelming, even for small and medium-sized manufacturers. Start by identifying key processes and developing clear, documented procedures for each one. From there, adopt an incremental approach:
- Focus on basic quality control measures initially, such as inspecting products for defects and standardizing production processes.
- Gradually integrate quality assurance practices to prevent defects.
- Invest in employee training to ensure everyone understands the importance of quality.
- Eventually, aim to comply with standards like ISO 9001, which can provide a clear framework for managing quality effectively. Smaller manufacturers may also benefit from using quality management software to streamline the process.
A QMS supports continuous improvement by promoting a culture of ongoing evaluation and optimization. By regularly monitoring key performance indicators (KPIs) like defect rates, production times, and customer feedback, a QMS identifies areas for improvement. The PDCA (Plan-Do-Check-Act) cycle is commonly used in QMS to test changes, evaluate results, and implement improvements. This focus on constant assessment and adjustment ensures that the organization remains agile, reduces waste, and continues to meet customer expectations over time.
Leadership plays a critical role in the success of a QMS. Without commitment from top management, a QMS is unlikely to be effective. Leaders must set the vision for quality management, communicate its importance to all levels of the organization, and allocate the necessary resources for implementation. Additionally, leadership is responsible for fostering a culture of quality by empowering employees to take ownership of processes and participate in continuous improvement efforts. When leadership is engaged and supportive, the QMS is more likely to be embraced by the entire organization and lead to lasting improvements in quality and performance.