Kaizen Philosophy: Unlocking The Power of Continuous Improvement
Abstract
Kaizen, a Japanese term meaning “change for the better,” is a philosophy that emphasizes continuous improvement in all aspects of manufacturing. It is not a one-time overhaul or dramatic change; instead, it focuses on making small, incremental improvements consistently over time. This method, pioneered by Japanese manufacturing giants like Toyota, has become a cornerstone of lean manufacturing, enabling businesses worldwide to increase efficiency, reduce waste, and enhance product quality.
The power of Kaizen lies in its simplicity and practicality. Unlike more complex management systems, Kaizen encourages every employee—from factory workers to top-level managers—to participate in the improvement process. By identifying small inefficiencies in workflows, equipment usage, or even communication, teams can implement low-cost, high-impact solutions that streamline operations. This involvement fosters a culture of collaboration, accountability, and innovation, where each employee feels responsible for contributing to the company’s success.
In manufacturing, Kaizen can improve production processes by eliminating waste (muda), optimizing workspaces (through the 5S methodology), and enhancing overall productivity. By focusing on long-term sustainability, rather than short-term fixes, Kaizen ensures that improvements are continually refined, leading to lasting operational excellence.
In this article, we explore the core principles of Kaizen, its application in manufacturing environments, and how it aligns with lean production methods. We will also delve into how businesses can harness the power of Kaizen to create a more efficient, productive, and employee-centered work environment. Through the lens of continuous improvement, Kaizen offers manufacturers a simple yet powerful approach to achieving operational excellence and staying competitive in an ever-evolving global market.
Keywords: Kaizen in manufacturing, Continuous improvement in manufacturing, Kaizen philosophy, Lean manufacturing Kaizen, Kaizen process improvement, Kaizen benefits in manufacturing, Kaizen methodology, Employee-driven improvement Kaizen, Kaizen and waste reduction, Kaizen in lean production, Incremental improvement in manufacturing, Kaizen 5S methodology, Operational excellence through Kaizen, Kaizen manufacturing strategy, Kaizen culture of improvement, Kaizen lean manufacturing examples, Kaizen manufacturing techniques, Kaizen workplace optimization, Small changes big impact Kaizen, Kaizen and manufacturing efficiency.
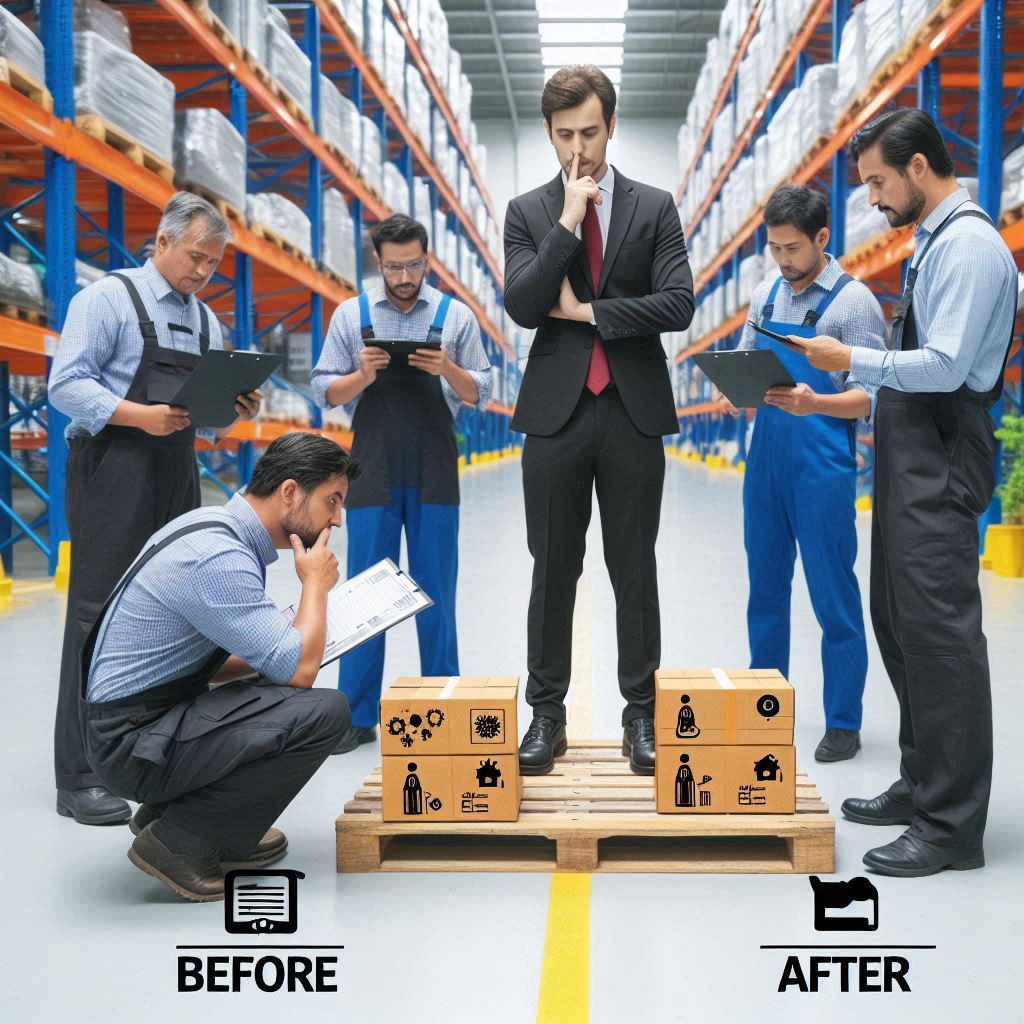
If you’ve ever looked at a seemingly well-oiled machine of a production line and thought, “How could this get even better?” – then you’ve already dipped your toes into the world of Kaizen. Originating in Japan, the term “Kaizen” means “change for the better” and is a philosophy that even the most efficient manufacturing processes can always be improved. And the best part? You don’t need a massive overhaul to see results; it’s all about making small, consistent changes.
1. The Heart of Kaizen: A Philosophy, Not Just a Tool
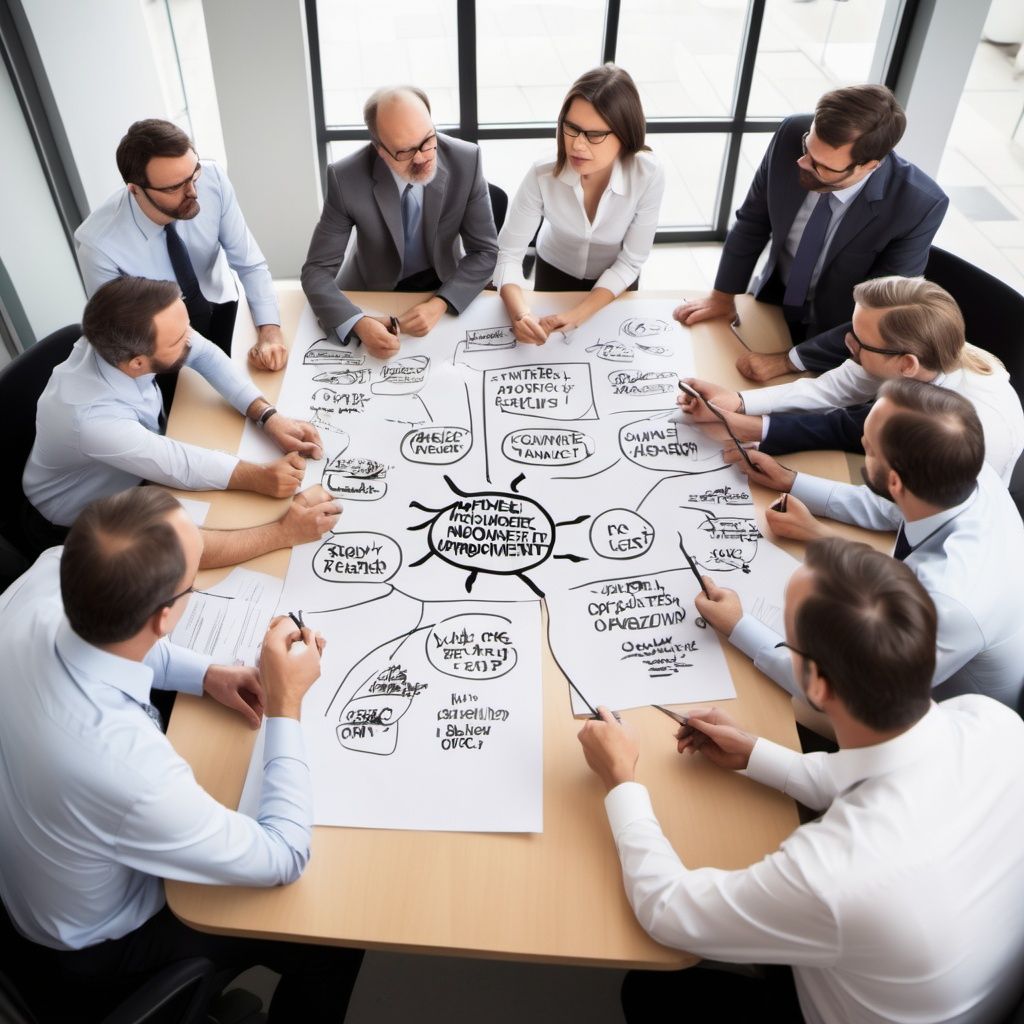
Kaizen isn’t just a fancy buzzword or a technique to implement once and forget about. It’s a mindset – a cultural shift toward thinking that improvement is never-ending. In the Japanese way of working, Kaizen is about nurturing the idea that even small tweaks can have a big impact. It emphasizes collective effort, involving everyone from floor workers to managers in identifying and solving problems.
When I first learned about Kaizen, I was struck by its simplicity. You don’t need complex software, expensive equipment, or elaborate methodologies to get started. All you need is the willingness to observe, question, and improve. This is one reason why Kaizen has become a cornerstone of manufacturing excellence around the world.
2. Core Principles of Kaizen: Small Changes, Big Results
At its core, Kaizen is driven by a few key principles:
- Continuous Improvement: The journey never ends. You might streamline one process today, but there’s always room for further enhancement tomorrow.
- Employee Involvement: Those closest to the work are often best positioned to identify inefficiencies. Kaizen empowers employees at every level to contribute ideas and insights.
- Gemba (Go to the Real Place): True problem-solving happens where the work is done. In manufacturing, this means being present on the factory floor, observing processes firsthand.
It’s easy to get caught up in high-level strategies while overlooking what’s happening on the ground. That’s why the principle of Gemba is so powerful – it reminds us that improvement starts with understanding the reality of the work environment.
3. How to Implement Kaizen: The PDCA Cycle
So, how do you actually put Kaizen into action? It all starts with the PDCA (Plan-Do-Check-Act) cycle. This four-step model is the engine behind Kaizen’s continuous improvement:
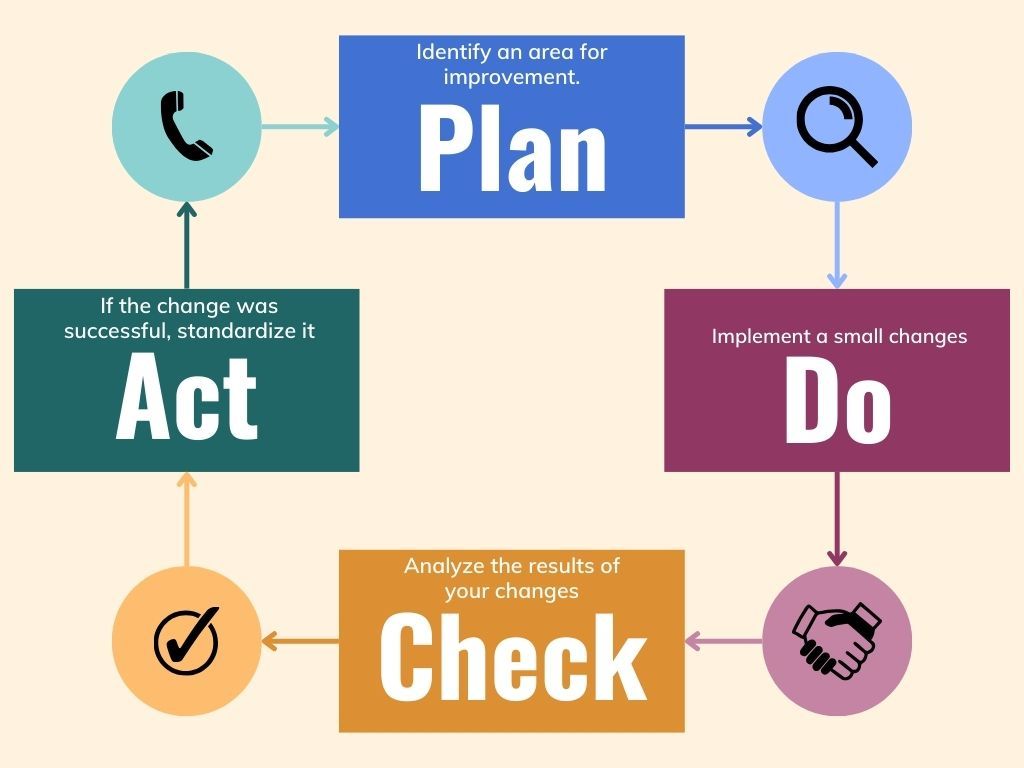
Plan: Identify an area for improvement. Maybe it’s a bottleneck on the production line or a repetitive quality issue. Gather data, talk to employees, and understand the root causes.
Do: Implement a small change. This could be adjusting a workstation layout to reduce employee movement or introducing a checklist for quality control.
Check: Analyze the results of your change. Did it reduce downtime? Are defects lower? This phase is crucial for understanding what works and what doesn’t.
Act: If the change was successful, standardize it. If not, learn from the experience and start the cycle again.
3. Kaizen Tools: 5S and Beyond
While Kaizen is a philosophy, there are practical tools that support it. One of the most widely used is the 5S methodology: Sort, Set in Order, Shine, Standardize, and Sustain. Implementing 5S on the factory floor can drastically improve efficiency by reducing clutter, organizing tools, and creating a clean, orderly work environment.
Another favorite tool is the “5 Whys” technique, which involves asking “Why?” repeatedly to drill down to the root cause of an issue. For example, if a machine keeps breaking down, you might ask: “Why did it break?” Maybe it wasn’t properly lubricated. “Why wasn’t it lubricated?” Because the maintenance schedule wasn’t followed. “Why wasn’t the schedule followed?” And so on, until you get to the heart of the problem.
4. The Benefits of Embracing Kaizen
What makes Kaizen truly special is its holistic impact. By continuously making small improvements, manufacturers can see tangible results:
- Reduced Waste: Kaizen focuses on eliminating waste in all forms – from excess inventory to unnecessary movement on the factory floor. Over time, this can result in significant cost savings.
- Enhanced Efficiency: Small changes, like streamlining workflows or reducing the number of steps in a process, add up. The cumulative effect is improved productivity and faster turnaround times.
- Higher Employee Morale: When employees are encouraged to participate in improvement efforts, they feel valued. This boosts morale, which can lead to increased motivation and creativity on the job.
5. Challenges of Implementing Kaizen
Of course, implementing Kaizen isn’t without its challenges. One of the biggest obstacles is resistance to change. Many employees, especially those who’ve been in the industry for years, might be skeptical of new methods. Here’s where leadership comes in – managers need to foster a culture where continuous improvement is valued and celebrated.
Another pitfall is lack of follow-through. It’s easy to initiate a Kaizen event, but the real work lies in maintaining and building on those changes. This is where the “Sustain” part of the 5S methodology becomes critical.
6. Real-World Kaizen Success Stories
I’ve seen Kaizen work wonders on the factory floor. In one case, a team I worked with used Kaizen to address a persistent bottleneck in their packaging line. By simply rearranging the layout to bring tools and materials within arm’s reach, they cut cycle time by 15%. I have been a kaizen practitioner and awarded many kaizen awards which resulted the automotive companies reduced their defect rate by encouraging operators to perform quick quality checks at each stage, catching errors before they compounded into bigger issues.
7. Getting Started with Kaizen: Quick Tips
If you’re new to Kaizen, start small. Look around your workspace and identify one thing that can be improved. Maybe it’s organizing tools or creating a simple checklist to ensure consistent quality. Implement the change, see how it works, and then move on to the next improvement.
Remember: Kaizen is about progress, not perfection. It’s the belief that no matter how well things are going, there’s always room for a little better.
Conclusion: Kaizen as a Way of Life – Lessons from Japan and Pakistan
There you have it – Kaizen in a nutshell! It’s not about grand gestures or overnight success; it’s about the steady, purposeful march toward excellence. And that’s something we can all strive for, one step at a time.
Kaizen isn’t a one-time fix; it’s a lifelong commitment to betterment. By embracing continuous improvement, manufacturers can create a more efficient, cost-effective, and fulfilling work environment. And from my experience working for 8 years in the automotive industry, I’ve seen the impact of Kaizen firsthand in both Japan and Pakistan.
In Japan, where the Kaizen philosophy was born, it has been deeply integrated into daily operations. I recall visiting a factory in Tokyo where even a small modification in tool placement on the assembly line led to a significant reduction in cycle time. By simply moving essential tools closer to the operator’s work area, they managed to reduce the process by a few seconds per unit. It may seem minor, but when you’re producing thousands of vehicles each day, those seconds add up to major gains.
In contrast, implementing Kaizen in Pakistan’s automotive industry has its unique challenges, mainly due to differences in workplace culture and resource availability. However, the potential for improvement is just as vast. For example, while working on a production line in Karachi, we noticed a recurring issue with material handling delays. By employing the “5 Whys” technique to dig into the root cause, we discovered that workers were spending excessive time searching for the right components due to poor storage organization. Applying a basic 5S approach (Sort, Set in Order, Shine, Standardize, Sustain), we restructured the storage area, significantly cutting down on wasted time and improving overall workflow.
These examples highlight that while the context might differ between Japan and Pakistan, the Kaizen philosophy remains universally applicable. It’s not about sweeping changes but about fostering a mindset where every employee actively seeks out small, incremental improvements. This commitment to continuous betterment, whether on the factory floors of Tokyo or Karachi, is what drives long-term success in manufacturing.
So, why wait? Get out on the shop floor, observe, ask questions, and start making those small changes. Remember, Kaizen is not just a tool; it’s a way of life. Whether in Japan or Pakistan, its principles of progress, not perfection, will steer your processes toward excellence, one step at a time.
One Comment